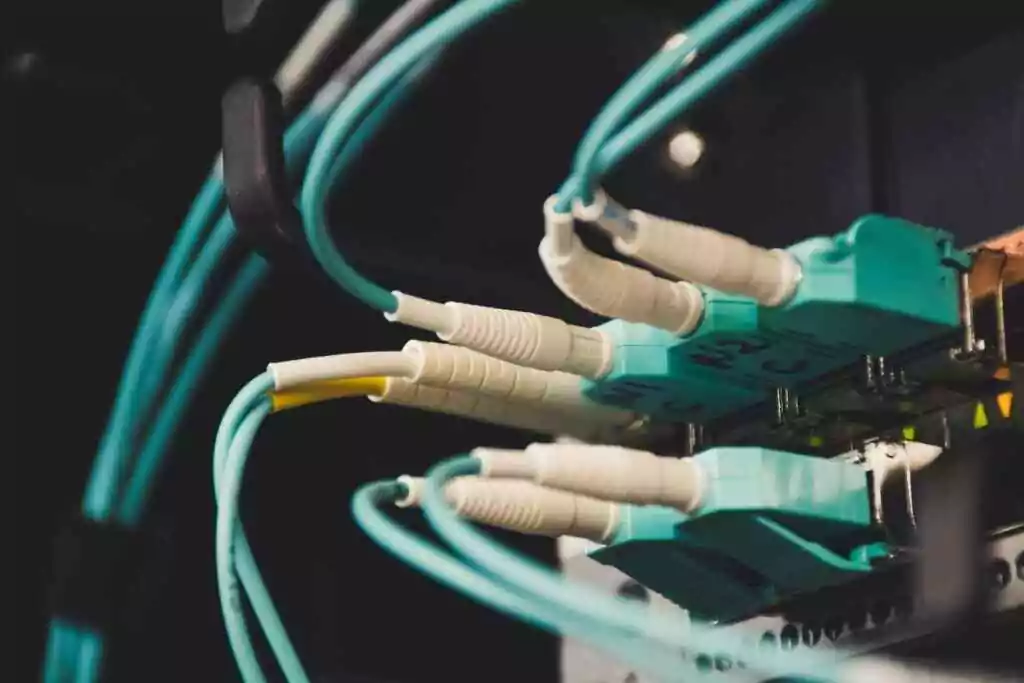
The cable manufacturing industry must address its major issue of talent gap formation because technological progress keeps accelerating. Traditional cable manufacturing methods transform modern smart production systems through the integration of Industry 4.0 elements that include automation together with IoT and AI and digital twins. Manufacturers need a workforce that combines skilled technicians with agents who have both learning adaptability and ongoing dedication to career development.
The development of cable manufacturing requires skilled professional recruitment and training alongside retention because it ensures the production of high-quality results operational effectiveness and innovative capacity. Cable industry organizations need to implement wide-ranging worker training and enhancement programs that teach the required competencies needed for achievement in digitalized manufacturing systems.
1. The Growing Talent Gap in Cable Manufacturing
New technology adoption has caused an emerging workforce challenge in the cable industry. The shortage of manufacturing talent stems from multiple reasons which include:
- Rapid Technological Change: Fast-evolving technology in smart manufacturing along with advanced quality control systems necessitates workforce capabilities that standard training methods do not supply.
- Aging Workforce: A majority of seasoned technicians approaching retirement have created an emptiness that beginners in the workforce find difficult to bridge.
- Specialized Skill Requirements: The labor market lacks personnel who possess specialized know-how for IoT, AI, and augmented reality technologies.
The success of cable manufacturers in competitive markets depends on addressing their talent shortage because they need to respond to modern infrastructure requirements.
2. Modern Training Strategies to Bridge the Talent Gap
To meet their talent requirements cable manufacturers establish modern educational methods which both enhance employee capabilities and recruit fresh personnel.
a) Digital and Virtual Training Platforms
- Virtual Reality (VR) Training: Training through Virtual Reality allows students to learn hands-on by experiencing real-world cable installation conditions through self-driving immersive sessions. Such training features a safe environment where workers can practice complex operations while remaining protected from actual job site risks.
- Online Learning Modules: E-learning platforms provide a flexible training system that students can use independently to learn about cable assembly basics and advance to digital diagnostics understanding. This training system is always available to students any time they need it.
- Augmented Reality (AR) for On-the-Job Assistance: AR applications overlay digital instructions onto the physical work environment, guiding technicians through cable installation and maintenance tasks with real-time support.
b) Continuous Professional Development Programs
- Certification and Accreditation: Standard certification programs deliver accreditation through systematic methods which result in improved professional competence throughout the industry. Professional accreditation of advanced manufacturing programs as well as quality control and digital maintenance instruction helps validate developer skills.
- On-the-Job Training and Mentorship: Mentors guide junior employees through on-the-job training programs which allow essential knowledge transfer between experienced workers and new recruits. Through mentorship programs organizations produce advanced skill sets and maintain their investigative expertise across their industry sector.
- Workshops and Seminars: Workshops and Seminars are conducted regularly to maintain worker knowledge about modern industrial trends which supports their continuous learning development.
c) Leveraging Industry 4.0 for Skill Enhancement
- Digital Twin Technology and 3D Simulation: Digital Twin Technology together with 3D Simulation functions let trainees conduct cable production simulations through virtual spaces so they can view and improve designs before creating physical prototypes.
- IoT and AI Integration Training: Training programs for websocket integration of IoT sensors and AI analytics must include a curriculum for data analytics along with predictive maintenance methods which are vital in modern cable manufacturing.
- Cross-Industry Collaboration: Learning best practices for training from the aerospace and automotive sectors gives valuable information about training methods during collaborative efforts. The adoption of joint training programs and inter-industry joint initiatives allows proven cable-making processes to be adapted for use in cable manufacturing.
3. Benefits of Bridging the Talent Gap
Implementing robust training and development strategies offers numerous benefits:
- Enhanced Productivity: Competent professional staff works with greater efficiency by lowering manufacturing mistakes and equipment downtimes.
- Increased Innovation: The continuous process of learning enables workforce members to become innovative which leads to the creation of new sustainable cable solutions and improved performance outcomes.
- Improved Safety: Safety improvements occur because trained employees learn safety protocols and the newest technological procedures alongside safety procedures which minimizes work-related incidents.
- Long-Term Competitiveness: Workforce development investments from companies produce ongoing competitiveness that sustains their growth efficiencies during market industry transformations.
- Sustainability: Modern training methods and digital tools support eco-friendly practices by reducing material waste and optimizing energy use throughout production processes.
Read Also: Where’s the Nearest HSBC Bank or ATM in Dubai? Find Now!
4. Case Study: Transformative Training in Cable Manufacturing
A prominent cable manufacturing company deals with older staff members and new technology barriers. The company created an extensive training methodology which used VR simulations together with online program learning and practical mentorship sessions. During this 12-month period the company achieved a 30% decrease in production errors as well as improved productivity and pleased workers. The company implemented digital twin technology along with AI analytics to decrease material waste and maximize energy efficiency which established new standards for contemporary cable manufacturing.
The thorough and complete training program demonstrated how it successfully filled industry requirements and achieved operational excellence in cable manufacturing.
5. Future Trends in Workforce Development
The future training approaches for cable manufacturing industry will include:
- AI-Driven Personalized Learning: The use of machines trained with artificial intelligence allows trainers to build voluntary educational programs which focus on individual requirements for the most efficient development.
- Global Collaborative Platforms: The emergence of digital global platforms enables workers to share knowledge across borders which boosts operational excellence through a highly competitive workforce.
- Advanced VR and AR Integration: Advanced VR and AR technologies will deliver practical and immersive training environments because of their ongoing development for application in training programs.
- Continuous Skill Assessments: Automated assessments and digital performance tracking will help identify training gaps, ensuring ongoing professional development.
Cable manufacturers can develop a job force using these latest trends which will adapt to present-day digitalized production operations.
Conclusion
The cable manufacturing industry requires the closure of its talent gap to preserve both business expansion and technological innovation initiatives. Carrying out complete training and development systems involving virtual reality learning and IoT predictive maintenance technology enables manufacturers to create better working conditions while boosting innovation and productivity rates.
Leading companies like Ducab are setting the standard by integrating advanced digital training methods and continuous professional development into their operations. With a commitment to building a highly skilled, adaptable workforce, the cable industry will continue to thrive in an increasingly competitive and technologically advanced landscape.